History
DEIF (Danish Electro Instrument Factory) was established in 1933 by Erling Foss and his two partners. The company’s main activity consisted in assembling and mounting by hand basic electromagnetic measuring instruments. Focus was on precision and robustness.
Today, the DEIF Group is fully owned by the founder’s son Toke Foss and his three children. The products have become extremely more advanced and markets now include knowledge intensive business areas such as Engine & Genset Controls, Switchboard Instrumentation, Bridge Instrumentation and Renewable Energy Controls. Yet, the focus on quality, reliability and service remains the same.
Production and development are located in Denmark, but DEIF sells and services its products worldwide.
To learn more about DEIF’s history, please see below.
The Early Years
Erling Foss was not particularly interested in technology. What really drove him was the determination to create value by means of technology. Following a brief career in F. L. Smidth, he made up his mind that a life of self-employment was the right thing for him.The early history of DEIF is closely associated with one man in particular: Erling Foss. As the son of one of the most significant Danish industrialists, Alexander Foss, Erling Foss was influenced by his father’s entrepreneurial spirit.
As fortune would have it, Erling Foss was contacted by two men with a business idea, but no money. The two men were Richard Dahl and Alex Juel-Hyllested. They both had a professional background from the company Helweg Mikkelsen – a leader in the market for electronic measuring instruments. They wanted to set up their own company and produce basic measuring instruments, e.g. ammeters, voltmeters, equipment for power plants, factories, hospitals etc.
Erling Foss believed in their project and decided to invest in it. On 1 June 1933, the three of them founded the company named Dansk Elektro Instrument Fabrik – DEIF.
The First Workshop
DEIF began as a craftsmanshop with a core of skilled workers such as instrument makers and occasionally watchmakers. The instruments were based on basic mechanics and mounted by experienced hands in order to ensure the best quality in the market.
Because of the need to be cost conscious, the first workshop – still far from a factory – was set up in the working-class district of Nørrebro in Copenhagen. It was located in a backyard on the first floor and took up no more than 150m2.
The biggest customers were power plants and switchboard builders such as Nordisk Elektro Apparatfabrik and Lauritz Knudsen. The aftershocks of the world crisis in the 1920’s were still felt, but the electricity supply continued to expand. The business cycles favoured DEIF.
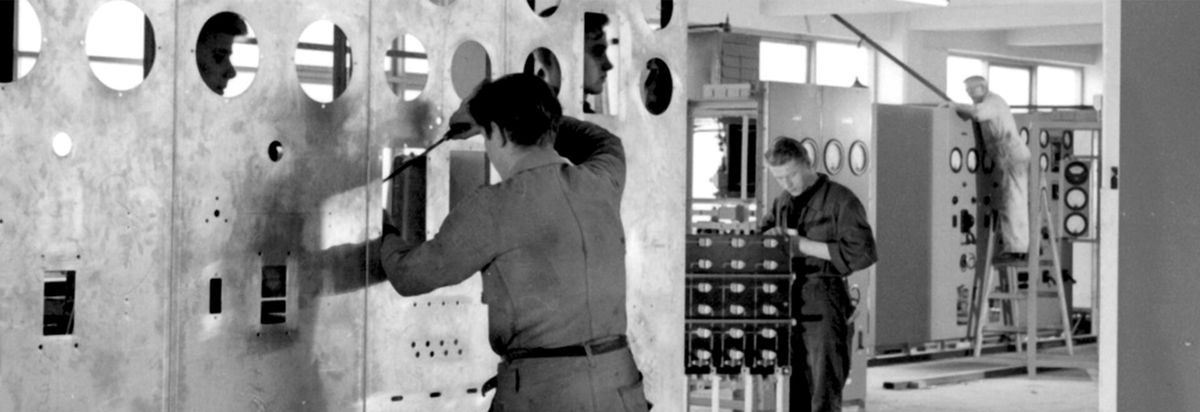
The Occupation
By 1940, the number of employees had reached 30. Opportunities for expansion were good. Therefore, on 9 April, DEIF decided to relocate to new and bigger facilities. The same day German troops invaded Denmark.
The occupation complicated the supply situation. But due to the demand from the arms industry, German manufacturers soon disappeared from the Danish market. This was fortunate for DEIF. Thus, production was suspended only on the days when workers had to return home because the workshop was too cold – fuel being the only acute scarcity during the occupation. DEIF was able to maintain full employment throughout the duration of the war.
From day one, Erling Foss was involved in the underground resistance movement. His reports to the allied intelligence services were a great help to them. But in 1944, he was forced to leave for Sweden with his family. The exile in Sweden made Erling Foss unable to continue as the Managing Director for DEIF. It therefore led to his resignation.
Surviving the 1940’s
Despite the end of the War on 8 May 1945, it took DEIF a few more years before trade was back to normal. But it would be another few more years before any real progress was felt.
The Marshall Plan was put together by the US to help the needy European economies back on foot. But because the US never played a role to DEIF’s business neither as a market nor as a supplier, aid from the US only had an indirect effect on DEIF.
Yet, in the period 1948-1952 Danish industry in general enjoyed a recovery due to the allocation of means deriving from the Marshall Plan. This meant work for electricians and table engineers – DEIF’s customers.
But for DEIF, the effect was delayed as the large-scale projects for which DEIF’s components were used, usually were planned well in advance. This is the reason why in 1949 the company for the first time experienced a decreasing order intake – paradoxically while the rest of the Danish economy was finally beginning to pick up.
A New Market
In 1950, Richard Dahl passed away and his assistant, Ove Neergaard, took over his responsibilities. Numerous of DEIF’s customers supplied shipyards and shipping companies and Neergaard continued Dahl’s work with great success.
The shipyard in Svendborg wanted to develop new electric rudder indicators for the bridges on their new ships. Within a very short time, DEIF developed a solution and secured an order worth DKK 125,000. The following year, the shipyard ordered some recently developed systems for automatic operation on board the ships. After a few years, the shipyards accounted for a significant part of the turnover.
It was to mark the beginning of a new business area – Bridge Instrumentation – that has been under constant development ever since. Today, DEIF controls half the world market and is the world’s number one supplier in this field.
Economic Upturn
The 1960’s were the decade of innovation. DEIF’s engineers began to utilise electronics for new product groups. Now it was possible to manufacture equipment for far more advanced solutions for industrial plants and ships than in the past.
In 1963, Louny Andersen took office as Managing Director. He reorganised and rationalised DEIF and results did not fail to appear. A year after his arrival productivity had increased by 50 percent.
Together with Ove Neergaard, Sales Manager and Head of Development, Louny pushed forward DEIF’s development. Among the most important projects was the temperature indicator for F. L. Smidth's gigantic pipe mills and revolving ovens.
Within a very short period of time, Louny had brought about great and important results for DEIF.
Relocation to Skive
In 1973, Thorsgade was no longer able to contain DEIF’s ambitions. There was too little room for the manufacture of electronics designed for the future.
In some regions of Jutland industrialisation was lagging behind. If DEIF were to relocate to one of those areas, inexpensive loans would be available through regional development funds. Nevertheless, it was a drawn-out process for Louny to find the right spot. But a competent and efficient effort on part of the municipality made the difference and the choice fell on Skive by the Limfjord.
Subsequently, DEIF moved its production to Skive. For the time being, development and sales were left behind in Copenhagen.
Everybody within the production department was invited to come along to Jutland. A handful of the most skilled workers were even directly encouraged to move to Skive. The ones who did not wish to move were helped to find jobs elsewhere in Copenhagen. Thus, the company avoided a mass exodus of workers.
Generator Controls
In 1973, the oil crisis led to vast increases in the price of oil. DEIF benefited from this development. New ships were often more inexpensive to run both in terms of manpower and fuel. Now that oil prices had become extremely volatile, newbuildings were begun all over the world. For this reason among others the company experienced an increase in turnover for electronic instruments amounting to more than 50 per cent.
The massive growth was a clear sign that DEIF was now competitive in the world market.
The development of the new electronic product group was to prove an important door opener to the growing marine industry. This was due to the useful qualities of the products as components in generator controls – and to the fact that DEIF’s agent in Norway, Carl Th. Malling, knew how to apply these qualities to ship equipment.
DEIF’s electronics were used for many of Carl Th. Malling’s solutions, e.g. if two generators were to be connected. The product developed for this purpose was later named ‘Delomatic’ (DEIF Logic Malling Technology). Today, generator controls for ships and land-based power generation have developed into DEIF’s main business activity.
Foss Follows Foss
In 1982, Erling Foss passed away and Toke Foss, his youngest son, took ownership of DEIF. Succeeding Louny as managing director, Toke Foss’ formal education included a degree in forestry and a diploma in business administration. Yet, modest business credentials did not keep the new company leader from initiating a large-scale reconstruction process, culminating in 1990 with the acquisition of Malling Kontrol.
Malling Kontrol was a developer and supplier of alarms, surveillance systems and other products for marine bridges. The takeover provided DEIF with the chance to put together a strong product portfolio in the marine business area, utilising the strengths of the Delomatic 2. The acquisition also gave access to customers in the marine market, with whom DEIF otherwise would not have come into contact. Among these were Malling Kontrol’s biggest customer, A.P. Møller-Mærsk.
Most important of all, though, was the volume increase and thus the higher earnings brought about by the takeover. Following a number of slow years, the company was now back to making money. A new era was about to begin.
Outsourcing
One factor in particular helped pave the way for the takeover of the marine company, Malling Kontrol: the outsourcing of labour.
For a long time, DEIF’s simple instruments had been relatively expensive to make. This was due to the comparably high hourly wages in Denmark. Toke Foss convinced the board that savings could be achieved by relocating the manufacture of basic instruments to a subcontractor in a less labour cost intensive country. The new partnership boosted DEIF’s finances and made the acquisition of Malling Kontrol possible.
A modern industry-based DEIF entered the 1990’s. But technological progress had left the company somewhat behind. Analogue electronics no longer sufficed for the tasks that new control systems had to perform. DEIF’s next generation of generator controls had to be altogether software-based. As a consequence, new engineers with knowledge of modern software and digital technology were taken on.
The development of a completely new computer-based genset controller went on for two years, but it was worth the wait: The third generation of the Delomatic was to propel DEIF into the top league of players in the market for marine generator contro
DEIF Expands
The Delomatic 3 was conceived as the backbone for a new flexible generation of generator controls. Before long, systems were sold to 25 percent of all new decentralised combined heat and power plants in Denmark. The success provided DEIF with the sustenance to continue the development of the system.
DEIF was serious about supplying energy solutions. As a consequence, the next strategic step was self-evident: To enter into the market for renewable energy. However, many factors had to be considered before attempting to develop a wind turbine genset controller. Indeed, the best solution seemed to be simply to acquire a company with the necessary expertise.
In 2004, Toke Foss came into contact with a small manufacturer of systems for wind turbines: West Control. The company was on the look-out for a bigger partner, who was able to offer both capital and knowledge. The timing was perfect.
DEIF took over West Control’s activities and moved them to Skive. Soon, renewable energy had become DEIF’s new product line.
Technologically, the acquisition of West Control provided important input in the development phase of Delomatic’s fourth generation. Thus, the Delomatic 4 became a shared platform for traditional genset controls and controls for wind and hydro generators. In 2006, the Delomatic 4 was introduced as DEIF’s solution for controlling the environmentally friendly energy sources of the future.
Past & Future
At a time when it is key to know the technology of tomorrow before everyone else does, DEIF’s decades of accumulated experience have proved invaluable.
The company’s transformation in the 1990’s brought about a more modern type of business. Today, the knowledge context of the products and their possibilities are crucial competition parameters. Low-price production alone no longer cuts it.
Illustrating this point, the development of genset controls helped turn DEIF into a global knowledge-based company. Thanks to the highly complex technological design of the products and the expert background of the developers, DEIF is now among the world’s biggest manufacturers of genset controls.
So, has DEIF lost touch with its roots as an instruments manufacturer? The answer is no. Although the company has moved on since its early days, the most basic analogue instruments from 1933 are still being sold with only slight modifications to the design. Moreover, DEIF still depends a great deal on the experience gained throughout the decades by the senior employees.
The latest innovation in illuminated bridge instrumentation is a good example of this: The X-coil instruments date back to the previous turn of century, but by applying already existing knowledge and adding a microprocessor it was possible to design an even more precise and stable instrument.
Thus, the circle in a way closes: In 1933, human capital was at the centre of DEIF when the first workshop was set up. Today, this resource is as vital as ever.